In our continuous quest to innovate and provide solutions that matter, I’ve turned our attention to a process that’s critical yet under-discussed in the solvent recovery spectrum – Ether Dehydration. This process is not just a technical necessity but a strategic advantage in the operational efficiency of industries reliant on ether solvents. Our journey through membrane separation technology, specifically through Pervaporation (PV) membranes, has led us to breakthroughs that are both environmentally sound and economically beneficial.
Ether dehydration is a pivotal step in ensuring the purity and performance of ether solvents used across various sectors. Using Damo’s PV membrane separation solution, we’ve set new benchmarks in achieving high-efficiency ether dehydration, leading to superior product quality with minimized environmental impact.
The need for such technological advancement is not just driven by the demand for high-purity solvents but also by the global imperative for sustainable industrial practices. As we navigate through this post, I aim to unfold the intricacies of ether dehydration, the pivotal role of PV membrane technology in this realm, and how Damo’s solutions are revolutionizing this critical process.
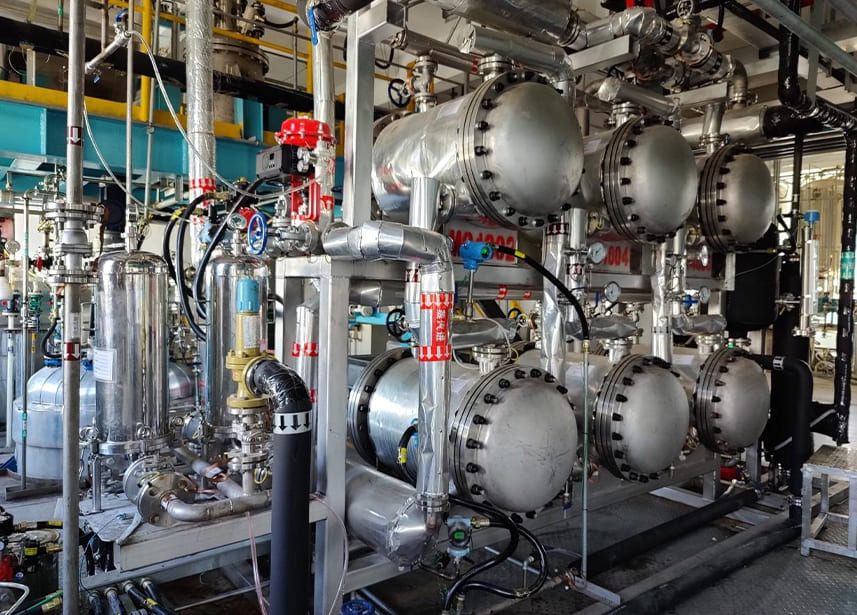
What Is Ether Dehydration and Its Significance in Industrial Applications?
Ether serves as a linchpin in several industries, underscoring its significance beyond being merely a solvent. Its roles in pharmaceuticals, fine chemicals, and a host of other critical applications spotlight the essential need for maintaining its purity and efficacy. This underscores the importance of ether dehydration – a process aimed at removing water to ensure ether retains its solvent quality and effectiveness in various industrial processes.
Traditional dehydration methods, while effective to a certain extent, often fall short of meeting the evolving demands of efficiency, environmental sustainability, and operational cost-effectiveness. These methods can be energy-intensive, less efficient, and sometimes even environmentally damaging due to the high temperatures required and potential chemical waste. In such a context, the advent of Pervaporation (PV) Membrane Separation technology, particularly our solution, marks a transformative approach to ether dehydration.
Our PV membrane technology offers a stark contrast to traditional methods by providing a solution that is not only seamless and highly efficient but also environmentally friendly. The technology utilizes a specialized membrane capable of selectively separating water from ether through a process that requires significantly lower energy inputs. This selective permeation ensures that the ether’s quality is not compromised, enhancing the efficiency of the subsequent industrial processes it’s involved in.
The significance of employing PV membrane separation for ether dehydration extends beyond the immediate benefits of solvent purity. It aligns with the broader industry objectives of reducing carbon footprints, minimizing energy consumption, and cutting operational costs. For industries such as pharmaceuticals where the purity of solvents directly impacts product quality and safety, the ability to achieve high levels of dehydration without compromising the ether’s integrity is invaluable.
Furthermore, our approach to ether dehydration with PV membrane technology is reflective of a commitment to innovation and sustainability. It addresses the pressing need for methods that not only meet but exceed environmental and efficiency standards. By choosing this path, we’re not just offering a solution for today but paving the way for more sustainable industrial practices in the future.
This focus on efficient, sustainable, and cost-effective ether dehydration is a testament to our dedication to meeting the needs of industries reliant on high-purity solvents. It’s an approach that not only addresses the current challenges but also anticipates the future needs of our clients, ensuring that they remain at the forefront of their respective fields.
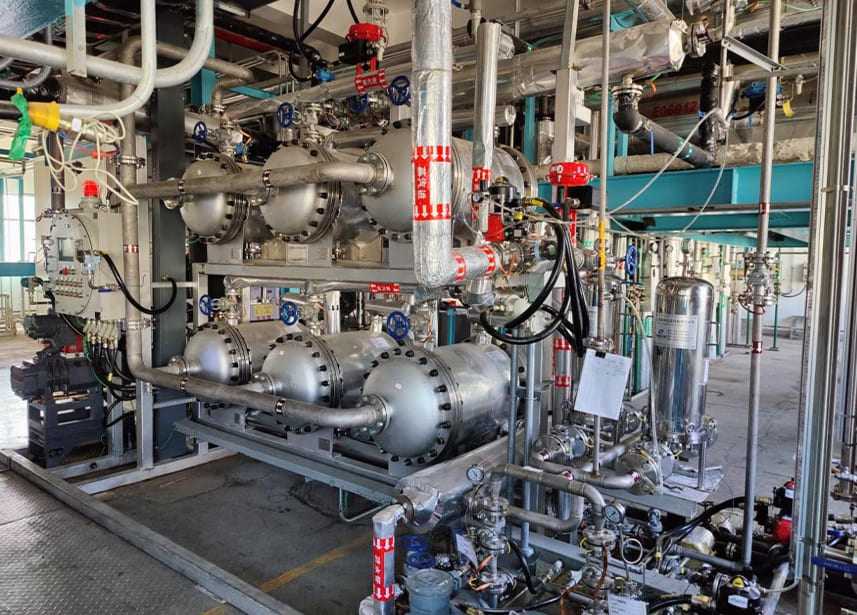
How Does Damo’s PV Membrane Separation Stand Out for Ether Dehydration?
In the realm of solvent recovery, particularly with ethers, the quest for more efficient, sustainable, and precision-focused dehydration methods has led to significant technological advancements. Among these, Damo’s Pervaporation (PV) Membrane Separation technology stands out as a beacon of innovation, especially tailored for the dehydration of ethers. This unique method significantly enhances the purity and efficiency of ether dehydration processes, setting a new standard in the industry.
Our approach, leveraging inorganic pervaporation membranes, is at the forefront of this transformation. These membranes excel in their selective permeability, allowing water molecules to pass through while retaining the ether solvent, thereby achieving a high degree of dehydration. The process operates at a molecular level, ensuring that even the minutest water particles are effectively removed from the ether solvent.
The benefits of utilizing Damo’s PV membrane technology for ether dehydration are manifold. Firstly, the unmatched purity levels attained through our system directly translate to improved quality and performance of the ether in various applications. This is paramount in industries where even minor impurities can compromise product integrity, such as pharmaceuticals and fine chemicals.
Moreover, our system’s efficiency in reducing energy consumption marks a departure from traditional dehydration methods, which are often energy-intensive and environmentally burdensome. By optimizing the dehydration process, we not only ensure operational cost savings but also contribute to environmental sustainability by minimizing the carbon footprint associated with ether solvent recovery.
Another standout feature of our PV membrane technology is its adaptability and scalability. Designed to meet the diverse needs of industries utilizing ether solvents, our systems can be tailored to specific operational capacities and requirements. This flexibility ensures that as your business grows and your needs evolve, our dehydration solution can adapt seamlessly, providing a sustainable solution that grows with you.
In addition, the operational simplicity and safety of Damo’s PV membrane systems cannot be overstated. With automation and advanced control systems, the dehydration process becomes more manageable and less prone to errors, ensuring consistent product quality and reducing the need for extensive manual oversight.
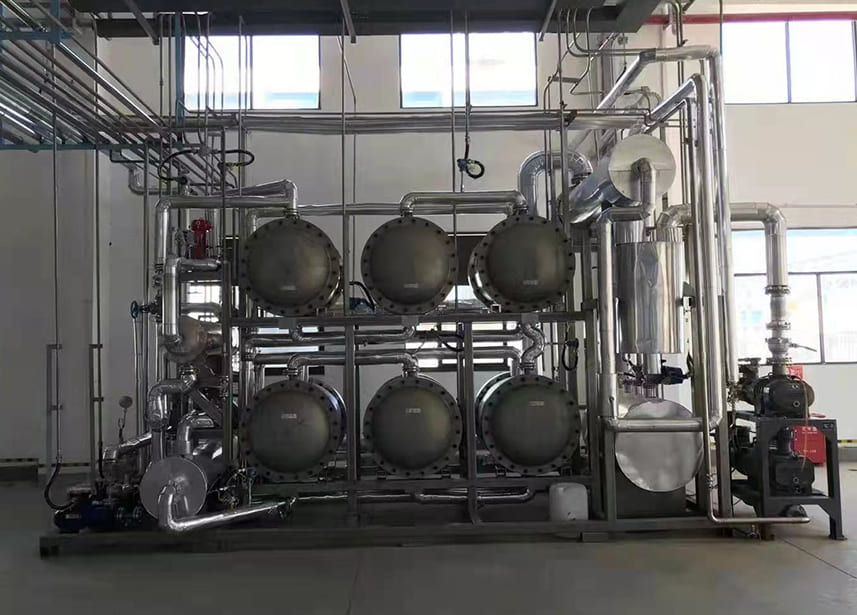
What’s the Advantages of Damo’s PV Membrane for Ether Dehydration?
Utilizing Pervaporation (PV) membrane technology for the dehydration of ether represents a paradigm shift in how industries approach solvent recovery, especially considering the stringent purity requirements and environmental regulations we face today. Here’s a deeper look at the myriad benefits our technology offers, underscoring our dedication to innovation and sustainability.
High Purity Levels
Damo’s membrane separation solution is engineered to achieve superior dehydration levels, attaining ether purity that is paramount for industries like pharmaceuticals and fine chemicals. This heightened purity ensures that the ether solvent’s effectiveness is maximized, contributing significantly to the quality of the end products. It’s a game-changer for processes that are sensitive to even the slightest contamination, providing their clients with the confidence that they are utilizing the best possible ingredients in their operations.
Energy Efficiency
The energy footprint of traditional dehydration methods has always been a concern, both economically and environmentally. Damo’s solution addresses this head-on, significantly lowering energy requirements for dehydration. This not only aligns with their commitment to sustainability by minimizing carbon emissions but also translates to considerable cost savings for the clients, making their operations more sustainable and efficient.
Operational Simplicity
We understand that complexity adds to operational costs and risks. Our PV membrane system simplifies the dehydration process, eliminating the need for intricate setups and the use of additional chemicals. This streamlined approach reduces both the risk of operational errors and the costs associated with complex process management. It’s about making things easier, safer, and more cost-effective for businesses striving to maintain their competitive edge.
Environmental Responsibility
In today’s world, environmental stewardship is not just a moral obligation but a competitive advantage. Our technology produces minimal waste and operates without the need for hazardous chemicals, showcasing our dedication to protecting the planet. By adopting our PV membrane system, businesses can significantly reduce their environmental impact, aligning with global sustainability goals and meeting the growing consumer demand for eco-friendly practices.
In summary, our PV membrane technology for ether dehydration is designed not just to meet the current needs of industries but to anticipate future challenges, providing a solution that is pure, efficient, simple, and responsible. It’s about delivering unmatched value while fostering a healthier planet.
What Are the Challenges and Solutions for Ether Dehydration Using PV Membrane Technology?
Integrating PV membrane technology into ether dehydration processes poses a set of unique challenges, reflecting the complexity and variability inherent in industrial-scale applications. The first challenge involves the scalability of PV membrane systems to accommodate large-scale industrial operations. This is crucial for ensuring that the technology can be effectively applied in settings that demand high volumes of ether dehydration without compromising efficiency or purity levels.
Another significant hurdle is the diversity of ether compositions encountered in industrial applications. Each type of ether, with its unique properties and impurity profiles, requires a tailored approach to dehydration to achieve optimal results. This variability demands a versatile solution capable of adjusting to different types of ether without sacrificing performance.
The response to these challenges has been multifaceted, focusing on continuous research and development (R&D) efforts aimed at enhancing the capabilities of PV membranes. This ongoing R&D work is vital for pushing the boundaries of what PV membrane technology can achieve, specifically in terms of membrane selectivity, durability, and resistance to fouling. By improving these aspects, the technology becomes more adaptable and effective across a broader range of applications and ether types.
Customization of solutions represents another critical aspect of addressing the challenges. Recognizing that a one-size-fits-all approach is insufficient for the varied demands of industrial ether dehydration, solutions are tailored to meet the specific requirements of each application. This bespoke approach ensures that each deployment of PV membrane technology is optimized for the particular type of ether being processed, leading to better dehydration outcomes and greater overall efficiency.
Conclusion
Ether dehydration transcends being merely a procedural step; it stands as a pivotal factor influencing both the quality and operational efficiency within sectors dependent on ether solvents. Damo Technologies takes pride in pioneering with its Pervaporation (PV) membrane separation solutions, seamlessly blending purity, efficiency, and environmental stewardship into a singular offering.