Table of Contents
In the realm of chemical processing, the push towards more sustainable and efficient technologies is more pertinent than ever. Among these, ethanol dehydration stands out as a process crucial for various industries, from biofuels to pharmaceuticals. Traditionally, this process has been energy-intensive and environmentally taxing. However, Damo Technology’s Pervaporation (PV) membrane emerges as a beacon of innovation, offering a new horizon of possibilities.
Damo’s PV membrane technology represents a paradigm shift in ethanol dehydration. By leveraging the molecular-sieving and surface-adsorption capabilities of zeolite and nanopore inorganic membranes, this technology offers a high-efficiency, low-energy, and environmentally friendly solution. It marks a significant stride towards sustainable chemical processing, promising over 99.95% recovery efficiency and substantial energy savings.
As we unpack the layers of this groundbreaking technology, let’s explore its mechanics, benefits, and real-world applications, underscoring why it’s becoming the go-to choice for forward-thinking industries.
What is Pervaporation, and Why is it a Game-Changer in Ethanol Dehydration?
Pervaporation is a sophisticated membrane separation technology that effectively separates components at a molecular level. Unlike conventional methods that rely on distillation or adsorption, pervaporation uses a selective membrane to separate water from ethanol, driven by vapor pressure differences. This not only ensures high purity levels but also dramatically reduces energy consumption, making it an attractive alternative for industries seeking greener solutions.
Expanding further, pervaporation fundamentally transforms the process of ethanol dehydration. This transformation is not just incremental; it’s revolutionary. The technology works by allowing only water molecules to pass through a selective membrane, leaving behind a more concentrated ethanol product. The mechanism is elegant in its simplicity yet profound in its impact. The membrane acts as a gatekeeper, ensuring only water molecules escape, which are then condensed and removed, resulting in highly pure ethanol.
But what truly sets pervaporation apart is its energy profile. Traditional methods of ethanol dehydration, such as azeotropic distillation, require significant amounts of energy to break the azeotrope between water and ethanol. This process is not only energy-intensive but also less efficient. In contrast, pervaporation operates at lower temperatures and pressures, translating to lower energy consumption and costs. This energy efficiency is a crucial factor in why pervaporation is heralded as a game-changer. By slashing energy requirements, it offers a more sustainable and cost-effective alternative, aligning perfectly with the industry’s and the world’s growing eco-conscious ethos.
Moreover, the quality of the product from pervaporation is unparalleled. The technology ensures that the ethanol produced is of high purity, meeting the stringent standards required in pharmaceuticals, food and beverage, and other industries. This level of purity is not just a benefit; it’s a necessity for industries that demand the highest quality standards.
Pervaporation is also incredibly versatile. It can handle various mixtures and compositions, proving effective even in complex separations where traditional methods falter. This versatility opens up a wide range of applications, making it a valuable tool in not just ethanol dehydration but in the broader spectrum of chemical processing.
In essence, pervaporation isn’t just improving the process of ethanol dehydration; it’s redefining it. Its impact extends beyond just the operational level to the strategic level, enabling industries to meet their sustainability targets, reduce operational costs, and produce higher quality products. As the world increasingly moves towards greener and more efficient technologies, pervaporation stands out as a beacon of innovation, leading the charge in the sustainable transformation of chemical processing.
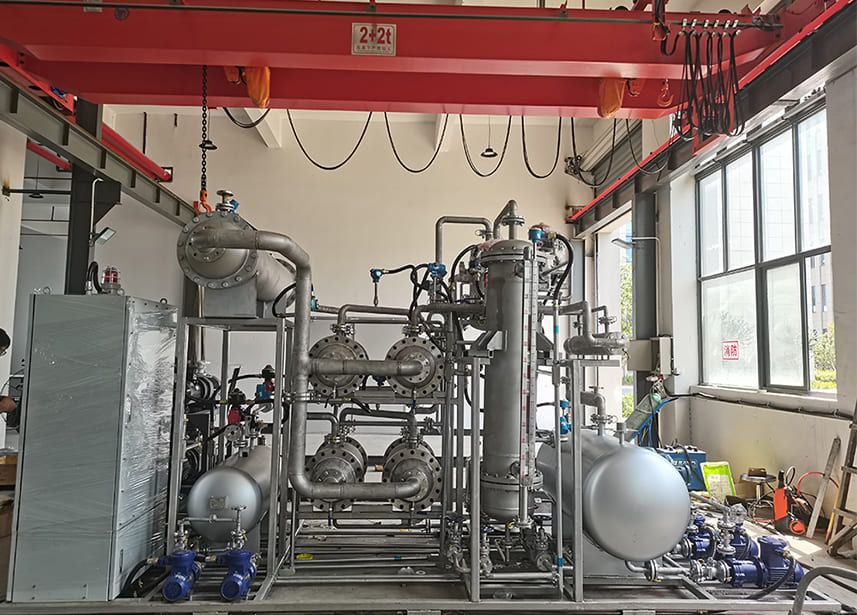
How Does Damo’s PV Membrane Work?
Damo’s PV membrane is engineered using zeolite molecular sieve and nanopore inorganic membranes. These membranes are supported on porous ceramic tubes, creating a dense layer that selectively allows water molecules to permeate while retaining ethanol. The process operates under mild conditions and doesn’t require additives, making it safe, clean, and energy-efficient. Furthermore, its acid resistance and operational stability ensure longevity and consistent performance, adding to its appeal.
To delve deeper into the workings of Damo’s PV membrane, it’s essential to understand the components and mechanics at play. The zeolite molecular sieve is a material with tiny, uniform pores. These pores are just the right size to allow water molecules to pass through while blocking larger ethanol molecules. This selectivity is the key to the membrane’s effectiveness. The nanopore inorganic membranes complement this by providing a robust and stable structure that can withstand the rigors of industrial processes. These membranes are not just barriers; they are finely-tuned instruments, engineered to perform a delicate balancing act.
The operational stability of Damo’s technology is another critical factor. Chemical processes can be harsh, with high temperatures, corrosive substances, and mechanical stress. The membranes used in Damo’s PV technology are designed to withstand these conditions, maintaining their integrity and performance over long periods. This durability means less downtime for maintenance and replacements, translating to higher efficiency and lower costs.
Moreover, the PV membrane operates under relatively mild conditions compared to traditional methods. This aspect is not just about energy efficiency; it’s about safety and environmental impact. Lower operating temperatures and pressures reduce the risk of accidents and decrease the plant’s thermal footprint. The absence of additives in the process further underscores its environmental credentials. By eliminating the need for potentially harmful chemicals, Damo’s technology ensures a cleaner process from start to finish.
The acid resistance of the membrane is another notable feature. Many chemical processes involve acidic or otherwise corrosive substances. Materials that can withstand these conditions without degrading are invaluable. Damo’s membranes offer this resistance, ensuring consistent performance even in challenging environments. This feature opens up a broader range of applications for the technology, making it suitable for various industries with different needs and requirements.
In conclusion, Damo’s PV membrane technology is a symphony of engineering, combining selectivity, stability, safety, and sustainability. Its operation is a testament to the power of innovation in the pursuit of more efficient and environmentally friendly industrial processes. As the industry continues to evolve, technologies like this will lead the way, offering solutions that meet the dual demands of economic viability and environmental responsibility.
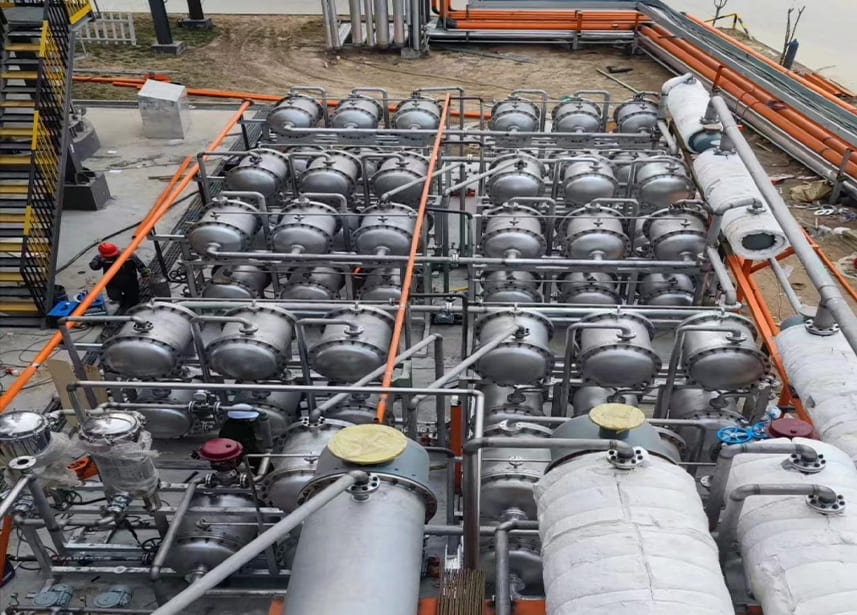
What Sets Damo’s Technology Apart?
- Energy Efficiency: Damo’s technology consumes significantly less energy than traditional methods, with liquid-phase dehydration consuming up to 0.15 tons of steam per ton of ethanol, compared to 0.45 tons for gas-phase dehydration.
- Environmental Impact: The process is free from additives and produces minimal waste, contributing to a cleaner, more sustainable operation.
- Cost-Effectiveness: With higher operational efficiency and lower energy requirements, the long-term cost savings are substantial.
- Flexibility: Suitable for both liquid-phase and gas-phase dehydration, it can be tailored to specific industry needs and integrated seamlessly into existing systems.
- Durability: The membranes offer excellent chemical and thermal stability, ensuring a longer operational life and reducing replacement frequency.
Damo’s technology isn’t just a step ahead; it’s a leap into the future of sustainable chemical processing. The energy efficiency of Damo’s PV membrane technology is a cornerstone of its design. In a world where energy costs and environmental impacts are increasingly under scrutiny, the ability to perform the same process with significantly less energy is a game-changer. This reduction in energy consumption doesn’t just lower costs; it aligns with global efforts to reduce carbon footprints and combat climate change, making it an investment in the future.
The environmental impact of industrial processes is a growing concern for companies and consumers alike. Damo’s technology addresses this head-on by minimizing waste and eliminating the need for harmful additives. This clean operation isn’t just about meeting regulations; it’s about setting new standards for what green technology can achieve. By reducing the ecological impact of ethanol dehydration, Damo’s technology helps companies not only improve their sustainability but also enhance their brand reputation and meet the expectations of eco-conscious consumers.
Cost-effectiveness is at the heart of Damo’s technology. With the rising costs of energy and materials, industries are under constant pressure to find more efficient and economical solutions. Damo’s technology offers just that, reducing operational costs through lower energy consumption and longer membrane lifespans. This cost-effectiveness makes the technology accessible and attractive to a wide range of companies, from small-scale operations to large, multi-national corporations.
Flexibility and adaptability are critical in the fast-paced world of industrial processing. Damo’s technology offers this in spades. Whether it’s liquid-phase or gas-phase dehydration, the technology can be tailored to fit specific needs and seamlessly integrated into existing systems. This adaptability makes it a versatile solution, suitable for a wide range of applications and industries.
Finally, the durability of Damo’s membranes is a testament to the quality and reliability of the technology. In industrial settings, where downtime can be costly, the robustness of these membranes ensures continuous operation and reduces the need for frequent replacements. This durability not only means less maintenance and lower costs but also a more reliable and consistent process, which is crucial for industries where quality and precision are paramount.
In summary, Damo’s technology stands out not just for one reason but for many. It’s a holistic solution that addresses energy efficiency, environmental impact, cost-effectiveness, flexibility, and durability. It’s not just a better way to do ethanol dehydration; it’s a better way to do business and a better way to care for our planet.
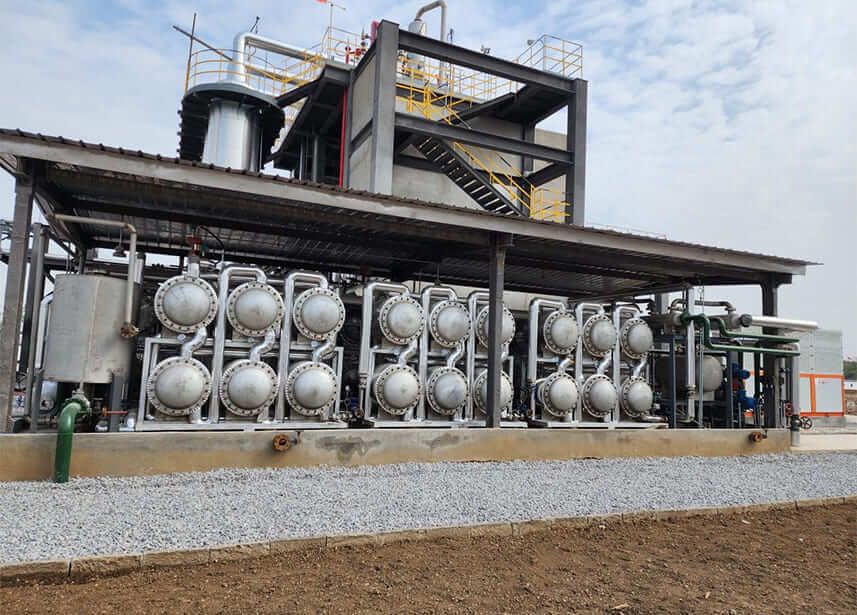
Real-World Impact: Success Stories and Applications
Damo’s PV membrane solution has been successfully implemented in various sectors, demonstrating its versatility and effectiveness. For instance, a biomedicine facility reported not only a 50% reduction in energy costs but also an enhanced quality of ethanol, crucial for their sensitive applications. Similarly, in the biofuels industry, companies have noted significant improvements in efficiency and cost savings, bolstering their sustainability goals.
The real-world impact of Damo’s technology is not just theoretical; it’s quantifiable and significant. Take, for example, a project involving a 1500 ton/year ethanol dehydration operation. By implementing Damo’s technology, this facility reduced water content from 15% to 0.2%, saving approximately USD$45,000 annually in energy costs compared to traditional distillation and adsorption technologies. This isn’t merely a reduction in costs; it’s a transformative shift in operational efficiency and sustainability.
Another striking example comes from a 5000 ton/year difluoroethanol dehydration project in Shandong, China. By utilizing Damo’s acid-resistant pervaporation membrane technology, the facility achieved water reduction from 4% to 0.05%, leading to an annual energy cost saving of about USD$220,000 compared to conventional methods. Moreover, a 6000 ton/year acetonitrile recovery project in Fujian, China, saw water content reduction from 80% to 1%, translating to an annual solvent recovery benefit of approximately USD$1.40 million.
These success stories underscore the real-world effectiveness of Damo’s technology. It’s not just about reducing costs or saving energy; it’s about revolutionizing entire processes and industries. The technology’s adaptability and efficiency have made it a preferred choice across diverse sectors, including biomedicine, new energy, fine chemicals, electronics, and environmental protection.
Beyond individual projects, Damo’s technology has broader implications for sustainability and efficiency in the chemical processing industry. By significantly reducing energy consumption, minimizing waste production, and ensuring high-quality output, Damo’s PV membrane is setting new standards for what’s possible in industrial operations. Its contribution to a more sustainable and efficient future is clear and growing.
In conclusion, the real-world impact of Damo’s PV membrane solution is a testament to its potential and performance. With each successful application, it’s proving to be an indispensable tool in the quest for more sustainable, efficient, and cost-effective industrial processes. As more industries adopt this technology, its role in shaping a greener, more efficient future becomes increasingly significant.
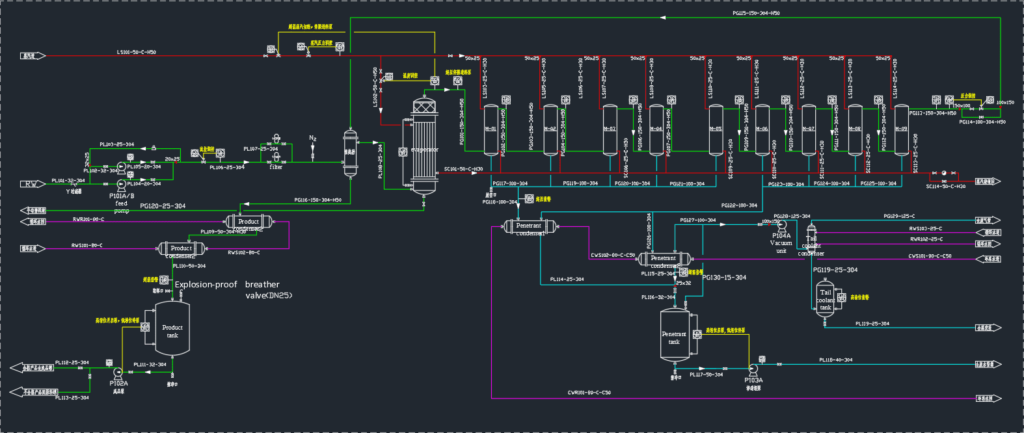
Navigating the Transition: Integrating Damo’s PV Membrane into Existing Systems
Integrating new technology into established processes might seem daunting. However, Damo’s technology is designed for ease of integration. Its modular design and compatibility with both liquid-phase and gas-phase systems make it adaptable to various scales and setups. Moreover, Damo offers comprehensive support, from pilot testing to after-sales service, ensuring a smooth transition and optimal performance.
The integration of Damo’s PV membrane into existing systems is a testament to its flexible and user-centric design. With a focus on safety, convenience, and efficiency, the technology is not just an addition to the process; it’s a seamless enhancement. The membranes are designed with full fluoropolymer, rubber, and graphene sealing gasket materials, offering durability and compatibility with a wide range of operational conditions. This adaptability means that the membranes can be fitted into existing systems with minimal adjustments, reducing the time and cost involved in the transition.
Damo’s approach to integration is holistic, considering not just the technical aspects but also the operational and economic implications. The technology’s low energy consumption, which is about half to one-third of that of traditional distillation methods, means that integrating it into existing systems can lead to significant cost savings in the long term. The initial investment is offset by the reduction in operational costs, making it a financially viable solution for many industries.
Moreover, the pervaporation process is simple and safe, with mild operating conditions and PLC automatic control, ensuring ease of operation and minimal risk. This simplicity is crucial during the transition phase, as it reduces the need for extensive training and reconfiguration of existing processes. The skid-mounted equipment further simplifies installation, making it a straightforward process that can be carried out with minimal disruption to ongoing operations.
Damo also offers a customized service process, tailoring the integration based on the specific needs and conditions of the client. This process includes site visits, communication, pilot testing, and after-sales follow-up service, ensuring that the technology is not just installed but also optimized for the best performance. The company’s commitment to providing long-term technical support and maintenance ensures that the systems continue to operate efficiently and reliably, offering peace of mind to clients.
In essence, integrating Damo’s PV membrane technology into existing systems is a journey towards enhanced efficiency, sustainability, and cost-effectiveness. With its adaptable design, comprehensive support, and commitment to client satisfaction, Damo makes this transition not just possible but also profitable and sustainable. As industries look to the future, technologies like Damo’s offer the tools needed to navigate the path towards a more sustainable and efficient world.
Conclusion
The Damo PV membrane represents not just a technological advancement but a revolutionary leap in the field of ethanol dehydration. It symbolizes a commitment to a future where sustainability and efficiency are paramount in chemical processing. This technology doesn’t just meet the industry’s demand for greener and more cost-effective solutions; it redefines it. By revolutionizing ethanol dehydration with unparalleled energy efficiency, environmental friendliness, and economic viability, Damo’s PV membrane sets a new standard. Embracing this technology is more than a smart business decision; it’s an investment in a sustainable and prosperous future for the industry and the planet at large.