Table of Contents
Are you tired of the recurring costs and environmental concerns associated with the annual purchase and disposal of Acetonitrile? You’re not alone. Many chemical engineers and procurement officers face these challenges.
Indeed, attaining 99.9% purity in Acetonitrile dehydration is both feasible and efficient, thanks to advanced technologies like Damo PV Membrane. This high level of purity meets stringent industry standards while also being environmentally sustainable.
Let’s dive into the details and explore how you can solve these pain points while optimizing your operations.
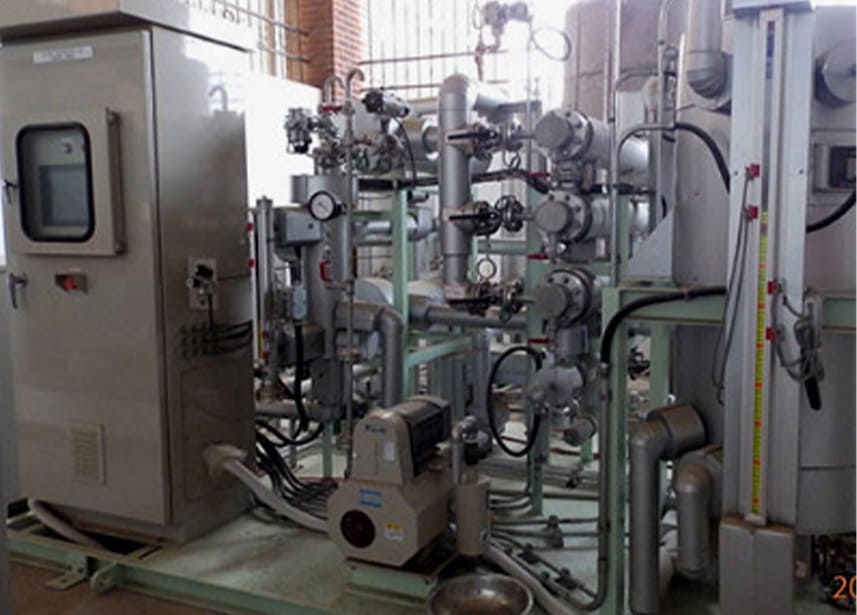
Why is Dehydration of Acetonitrile a Challenge?
Dehydrating Acetonitrile to 99.9% purity is a multifaceted challenge that extends beyond mere water removal. It demands a focus on efficiency, sustainability, and cost-effectiveness, which are often at odds in traditional methods. For instance, distillation, a commonly used technique, is notorious for its high energy consumption and environmental impact. The process often requires large amounts of steam and electricity, leading to inflated operational costs. Additionally, distillation produces waste liquid that poses disposal challenges and environmental concerns.
Enter Damo PV Membrane technology, a revolutionary solution that addresses these challenges head-on. Unlike distillation, our patented technology is designed for efficiency and sustainability. It consumes significantly less energy, requiring less than 0.5 tons of steam for 1 ton of solvent solution. This not only reduces operational costs but also minimizes the carbon footprint.
Moreover, Damo PV Membrane technology eliminates the need for waste liquid disposal. The technology is engineered to be environmentally friendly, aligning with modern sustainability goals. This is a crucial advantage, especially for companies looking to adhere to stringent environmental regulations.
In summary, the challenges in dehydrating Acetonitrile to 99.9% purity are not insurmountable but do require a shift from traditional methods to more advanced and sustainable technologies like Damo PV Membrane.
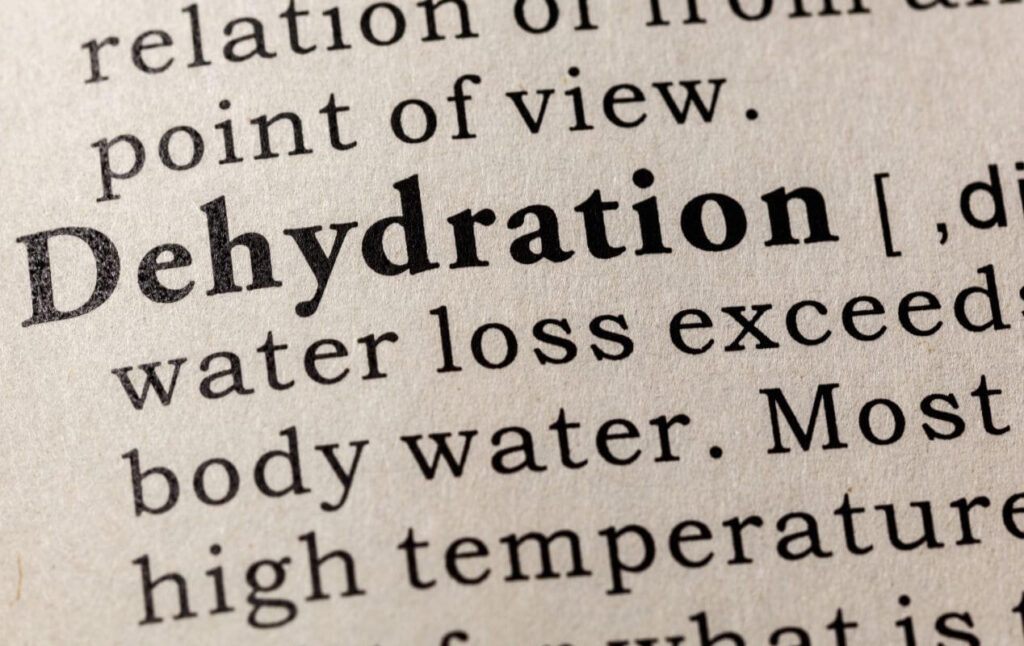
What Makes Damo PV Membrane the Ideal Solution?
When it comes to dehydrating Acetonitrile to 99.9% purity, Damo PV Membrane technology stands out as the optimal choice for several compelling reasons:
Efficiency
First and foremost, the technology is highly efficient, capable of reducing water content to less than 0.05%. This level of efficiency is unparalleled in traditional methods and ensures that you meet the highest industry standards for purity.
Energy-Saving
Damo PV Membrane is designed to be energy-efficient, consuming less than 0.5 tons of steam for 1 ton of solvent solution. This is a significant reduction compared to traditional distillation methods, which are notoriously energy-intensive. The energy savings translate directly into cost savings, making it a financially viable option.
Environmental Benefits
The technology is also environmentally friendly. Unlike traditional methods that require additional components for azeotropic dehydration systems, Damo PV Membrane eliminates this need. This not only simplifies the process but also aligns with sustainability goals, a critical factor in today’s regulatory landscape.
Safety
Safety is another area where Damo PV Membrane excels. The entire process is automatically controlled and monitored online with a Programmable Logic Controller (PLC), ensuring that the system operates within safe parameters at all times.
In summary, Damo PV Membrane technology offers a comprehensive solution that addresses the challenges of efficiency, energy consumption, environmental impact, and safety. It is not just an alternative but an advancement over traditional methods, making it the ideal solution for Acetonitrile dehydration.
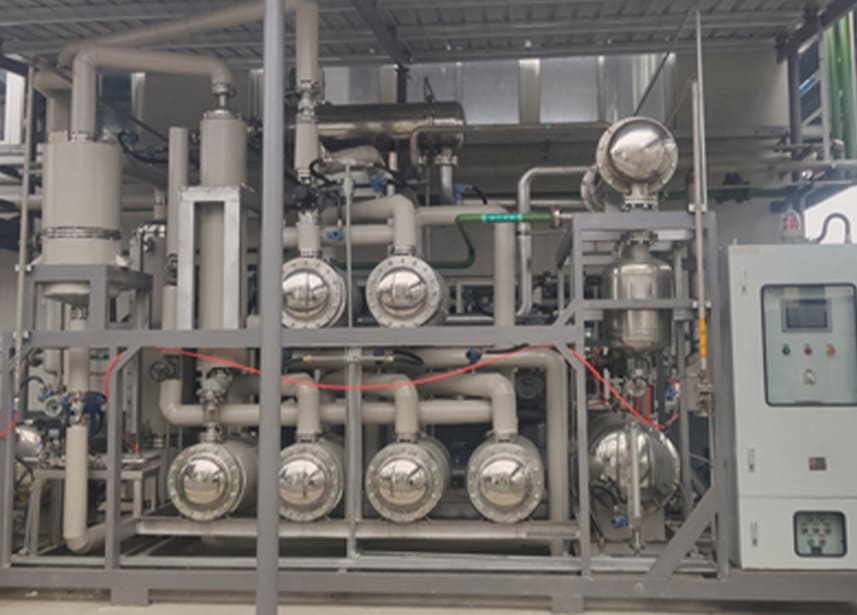
How Does the Damo PV Membrane Process Work?
Understanding the Damo PV Membrane process for Acetonitrile dehydration is crucial for chemical engineers and procurement officers aiming for optimal results. The process is designed for simplicity, efficiency, and effectiveness. Here’s a step-by-step breakdown:
Filtration
The first step involves filtering the raw Acetonitrile solution to remove any solid particles. This is essential as solid particles can damage the permeation membrane, affecting the overall efficiency of the process.
Preheating
Once filtered, the Acetonitrile solution undergoes preheating. This step is designed to recycle heat from the dehydrated product, contributing to energy efficiency. Preheating prepares the solution for the next stage while minimizing energy consumption.
Vaporization
The preheated material is then vaporized in an evaporator using steam. This is a critical step as it prepares the solution for membrane separation. The use of steam in this stage is optimized to ensure minimal energy consumption.
Separation
The final and most crucial step is the membrane separation. The vaporized material passes through the Damo PV Membrane, which effectively removes water, achieving up to 99.9% purity. Learn more about membrane separation.
In summary, the Damo PV Membrane process for Acetonitrile dehydration is a well-orchestrated sequence of steps, each contributing to the overall efficiency and effectiveness of the operation. It’s a streamlined approach that addresses both operational and environmental concerns, making it a superior choice for Acetonitrile dehydration.
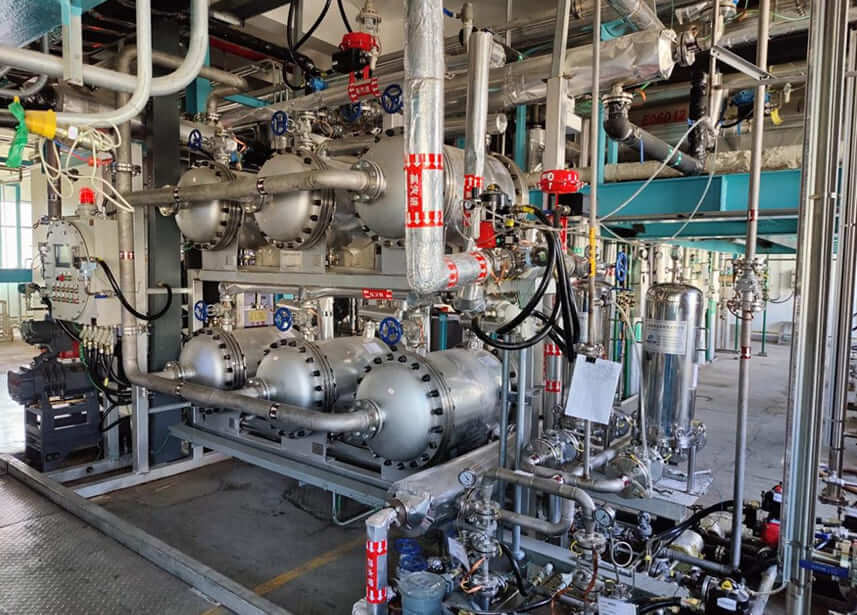
What Equipment is Required?
For those considering implementing Damo PV Membrane technology for Acetonitrile dehydration, understanding the required equipment is essential. Each piece of equipment serves a specific purpose and contributes to the overall efficiency and effectiveness of the process. Here’s a detailed look at the major equipment components:
Pump
The pump is responsible for transporting the raw Acetonitrile solution to the filter. It ensures a consistent flow rate, which is crucial for maintaining the efficiency of the subsequent steps.
Filter
The filter is the first line of defense against solid particles that could potentially damage the membrane. It is designed with a pore size of around 0.5μm to effectively remove any impurities.
Heat Exchanger
The heat exchanger serves to preheat the filtered material, recycling heat from the dehydrated product. This not only prepares the solution for vaporization but also contributes to energy efficiency.
Evaporator
The evaporator is where the preheated material is vaporized using steam. This step is critical for preparing the solution for membrane separation and is optimized for minimal energy consumption.
Membrane Separator
The membrane separator is the heart of the Damo PV Membrane process. It utilizes our patented acid-resistant nanopore dehydration membrane to achieve up to 99.9% purity in Acetonitrile.
In summary, each piece of equipment in the Damo PV Membrane technology is engineered for maximum efficiency and effectiveness, ensuring a streamlined and cost-effective Acetonitrile dehydration process.
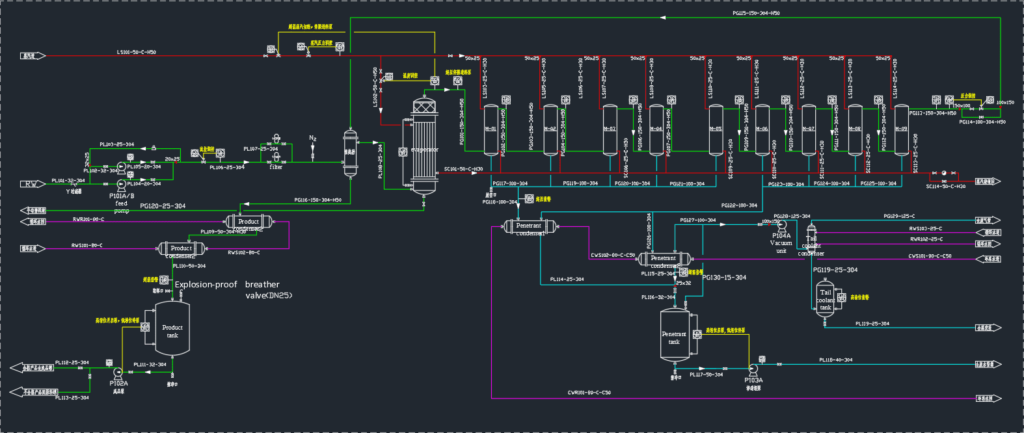
Are There Any Limitations?
While Damo PV Membrane technology offers a plethora of advantages, it’s crucial to be aware of certain limitations to make an informed decision. Here are some key points to consider:
Solid Particles
One of the primary limitations is that the raw material must be free of solid particles. Solid particles can damage the permeation membrane, affecting the overall efficiency and effectiveness of the dehydration process. Therefore, a robust filtration system is essential before introducing the raw material into the system.
Maximum Work Pressure
Another point to consider is the maximum work pressure for the equipment, which is not specified in the provided texts. This could be a factor depending on your operational requirements and may necessitate additional engineering considerations.
Utility Conditions
While the technology is designed for efficiency, it operates under specific utility conditions like steam pressure and electricity voltage. Adhering to these conditions is crucial for optimal performance.
Environmental Factors
Although Damo PV Membrane technology is environmentally friendly, it’s essential to ensure that it aligns with your organization’s sustainability goals and local environmental regulations.
In summary, while Damo PV Membrane technology offers a highly efficient and sustainable solution for Acetonitrile dehydration, it’s essential to consider these limitations. Proper planning and engineering can mitigate these factors, ensuring a successful implementation of this advanced technology.
How to Get Started?
Embarking on your journey with Damo PV Membrane technology for Acetonitrile dehydration is a straightforward process designed for your convenience. Here are the steps to get you started:
Visit Our Product Page
The first step is to visit our product page, where you’ll find detailed information about the technology, its features, and benefits. This will give you a comprehensive understanding of what we offer.
Contact Our Team
Once you’ve familiarized yourself with the product, the next step is to get in touch with our expert team. We provide customized solutions tailored to your specific needs, ensuring that you get the most out of our technology. Contact us for a customized solution.
Initial Assessment
Our team will conduct an initial assessment of your requirements, including the volume of Acetonitrile you need to dehydrate, your facility’s capabilities, and any specific challenges you may face.
In summary, getting started with Damo PV Membrane technology is a seamless process aimed at providing you with the most efficient and effective Acetonitrile dehydration solution. Reach out to us to take the first step towards a more sustainable and cost-effective operation.
Conclusion
Dehydrating Acetonitrile to 99.9% purity doesn’t have to be a daunting task. With Damo PV Membrane technology, you can achieve this efficiently, sustainably, and cost-effectively. Take the first step towards optimizing your operations today.
That’s it. For more information, feel free to reach out to us.