Table of Contents
Are you an engineer or a purchasing manager in a chemical plant or pharmaceutical factory? Are you looking for a reliable and efficient solution for ethanol dehydration? The Damo PV Membrane is designed to meet your needs, offering significant cost savings, reduced energy consumption, and a sustainable approach to ethanol dehydration.
The Damo PV Membrane is a state-of-the-art solution for 200 LPH Ethanol Dehydration. It efficiently separates water from ethanol, resulting in a product with less than 1% water content. This technology is energy-efficient, environmentally friendly, safe, simple to operate, and designed for continuous, round-the-clock operation.
In this guide, we will delve into the technical aspects of the Damo PV Membrane, highlighting its operational parameters, technological advantages, and why it stands out as the ultimate solution for ethanol dehydration in your facility.
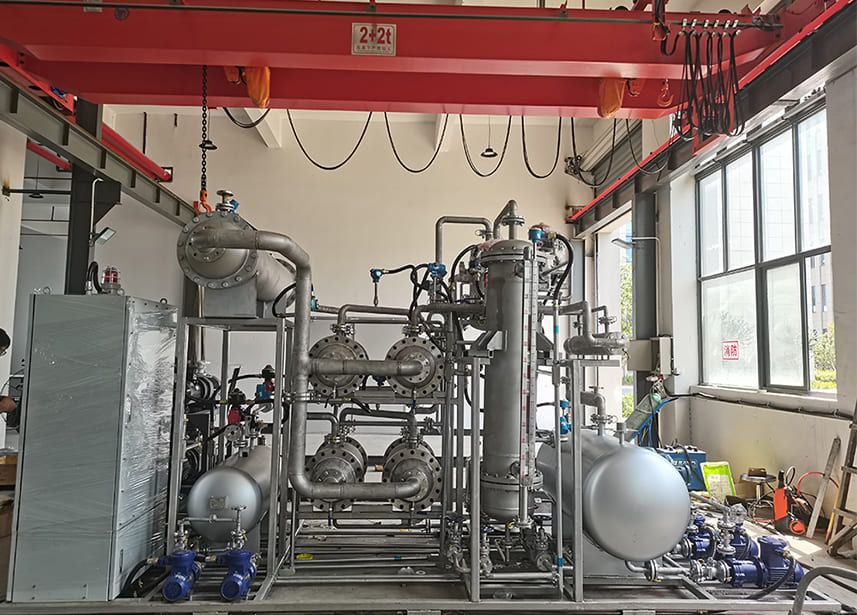
Technology Introduction
The Damo PV Membrane employs inorganic pervaporation technology, a process that effectively separates water from organic solvents through surface-adsorption and molecular-sieving mechanisms. The pore size of the permeation membrane (0.4 nm) is strategically designed to be between the molecular size of water and organic solvents, allowing for efficient water removal from the ethanol solution.
Operational Excellence and Energy Efficiency
The Damo PV Membrane operates at a temperature range of 100-140℃ and a pressure range of 0.1-0.3 MPa, ensuring optimal performance. One of its standout features is its energy efficiency. For every ton of solvent solution processed, it commonly consumes less than 0.5 tons of steam. This translates to significant savings on energy costs for your facility.
Environmental and Safety Benefits
The Damo PV Membrane is designed with environmental sustainability in mind. Unlike traditional methods, it does not require the introduction of other components for azeotropic dehydration systems. The process is controlled automatically and monitored online through a PLC and HMI, ensuring safety and simplicity.
Simplified Installation and Compact Design
The equipment is modular and has a small footprint. This compact design allows for easy integration into existing systems, minimizing the need for extensive site preparation and reducing installation costs.
200 LPH Ethanol dehydration Case By Damo PV Membrane Solution
Information for raw materials
Total Mass Rate: 200 L/hr | ||
Composite | Ethanol (%) | ≥60 |
H2O (%) | ≤40 | |
Product | H2O (%) | ≤1 |
Operation Parameters for Equipment
1 | Work Temperature(℃) | 100~140 |
2 | Work Pressure(MPa) | 0.1~0.3 |
3 | Product Temperature (℃) | ≤40 |
4 | Vacuum degree | ≤-99 kPa |
5 | Equipment explosion-proof level | dIIBT4 |
6 | Operation mode | Round the clock |
Feed Conditions
The pH of raw material is in the range of 6.5 to 8.5 (In fact, the maximum range can be PH2.0-8.5). The conductivity of raw material is less than 5 μS/cm. In addition, without of polymer, salts, saccharides, solid particles, acidity, alkalinity etc, which will damage permeation membrane in the raw material.
Technical Process Description
Raw Material Transport: The ethanol solution is precisely transported to a filter (with a pore size of around 0.1 μm) by a pump.
Preheating: The filtered material is preheated in a heat exchanger to recycle the heat from the dehydrated product.
Evaporation: Subsequently, the material is vaporized in the evaporator by steam.
Separation: The vaporized material flows into the membrane separators for dehydration. In this project, there are five membrane separators arranged in series.
Water Removal: The water molecules selectively permeate through the membrane under a pressure difference and are collected in a storage tank by the cooled condenser.
Water Transport: The collected water is then transported to the next process by a pump.
Product Cooling and Storage: The product produced by the membrane is cooled and collected in a storage tank.
Product Transport: The cooled and collected product is transported to the next process by a pump.
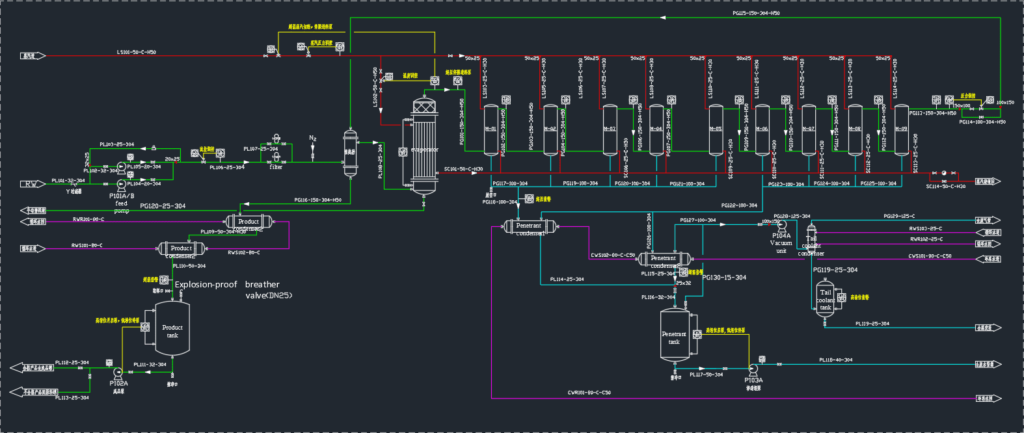
Consumed Costs
Category | Specification | Consumption per ton | Unit price | Cost |
steam | ≥0.3MPa | 0.6t | $30 | $18 |
electricity | 380V,50Hz | 50kWh | $0.1 | $5 |
circulating water | ≥0.3MPa,T≤32℃ | 15t | $0.03 | $0.45 |
Chilled water | ≥0.3MPa,T≤5℃ | 65m3 | $0.1 | $6.5 |
instrument air | ≥0.4MPa,dew-point≤-40℃ | ~4.5 m3 | – | – |
nitrogen | ≥0.20MPa | – | – | – |
Delivery Date
Within 120 days of effectiveness of contract
Equipment Footprint
Length * width * height =5500mm×2000mm×3600mm
Technical Information Directory
Damo provides comprehensive technical support, from process flow diagrams to equipment lists and operating procedures. Additionally, Damo is committed to training your staff, ensuring they are proficient in equipment structure, maintenance, control, and operation.
S/N | Technical Services | Response to Service |
1 | Process flow diagram | Submitted with the technical plan |
2 | Main equipment drawings | Submitted within 20 days after contract signing |
3 | Equipment List | Provided with each delivery |
4 | Debugging | Completed promptly after debugging conditions are met. |
5 | Operating procedures & maintenance | Provided with each debugging |
6 | Technical Information | Provided with delivery |
7 | Personnel Training | Performed concurrently with debugging, to ensure trainees are proficient in equipment structure and maintenance, equipment control, and operation. |
The Future of Ethanol Dehydration
As industries continue to seek sustainable and efficient solutions, the Damo PV Membrane represents the future of ethanol dehydration. It offers a high one-time recovery rate (>99%) and a membrane tube guaranteed for 2.5 years, promising long-term reliability and performance.