Isopropanol dehydration challenges? Damo Technology offers a reliable solution for a Hunan-based company. With an annual production capacity of 1,500 tons, Damo’s vapor-phase equipment dehydrates Isopropanol efficiently, delivering outstanding results. The innovative technology reduces water content from 15% to an impressive 0.5%, ensuring high-quality Isopropanol production. With a remarkable product recovery rate of up to 99%, Damo’s solution offers unparalleled efficiency and productivity.
The system has been operating stably for over a year, demonstrating its robustness and reliability. Damo’s innovative solution employs cutting-edge vapor-phase equipment that utilizes advanced membrane separation technology. With its proven track record in the industry, Damo’s solution offers a cost-effective and efficient alternative to traditional dehydration methods. Experience exceptional results in your Isopropanol production process with Damo’s reliable and innovative solution.
Find out more about Damo Technology’s advanced dehydration process and the key benefits it offers, including energy efficiency, safety, and high product recovery rates.
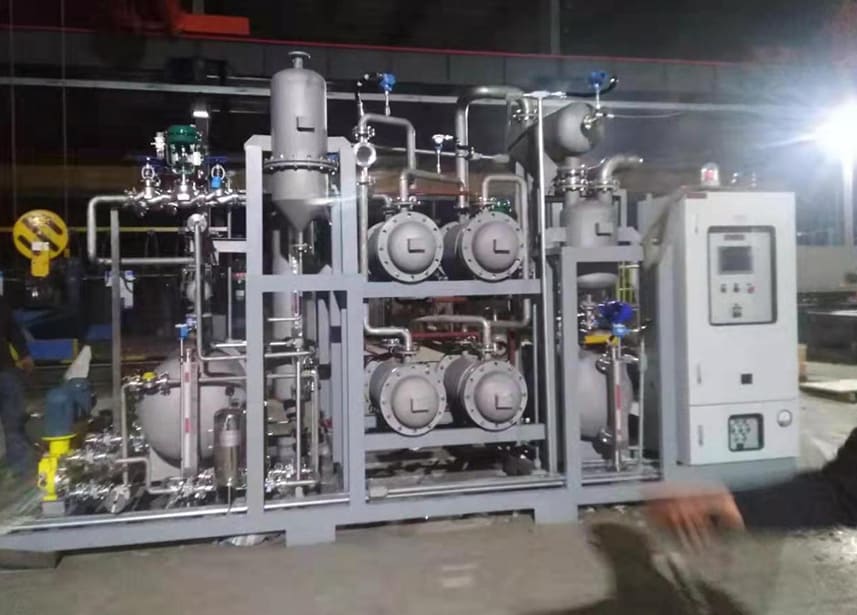
The Innovative Dehydration Solution by Damo Technology
Damo Technologies offers a cutting-edge dehydration process that effectively removes water from isopropanol using gas-phase equipment. With this innovative technology, the highest dehydration effect can reach an impressive 99.995%. This level of efficiency ensures high-quality and reliable Isopropanol production.
Moreover, Damo Technology is the only company capable of dehydrating organic acids above PH2 effectively. The advanced membrane separation technology used in Damo’s solution ensures the highest level of precision and efficiency. This breakthrough technology offers a cost-effective and environmentally-friendly alternative to traditional methods of Isopropanol dehydration.
With Damo Technology’s solution, you can expect outstanding results in your Isopropanol production process. The system’s efficient and reliable performance, coupled with its high dehydration rate, ensures that you can produce high-quality Isopropanol without any hitches. Damo’s commitment to innovation and sustainability means that you can benefit from the latest technology in the industry while minimizing your impact on the environment. Choose Damo’s solution for unparalleled efficiency and productivity in Isopropanol dehydration.
Advantages of Damo Technology’s Dehydration Process
Energy efficiency
The advanced dehydration process developed by Damo Technology consumes less energy compared to traditional methods, making it a more sustainable and cost-effective solution for the chemical industry.
Safety
The vapor-phase equipment and the process employed by Damo Technology ensure a safe working environment, minimizing the risk of accidents and adhering to industry safety standards.
High product recovery rates
The innovative dehydration process achieves an impressive product recovery rate of up to 99%, ensuring that the company maximizes its output and profitability.
Stable operations
Damo Technology’s dehydration solution has been operating stably for over a year at the Hunan-based company, demonstrating the reliability and effectiveness of this advanced process.
Customizable solutions
Damo Technology can tailor its dehydration processes to meet the specific requirements of different companies and industries, ensuring the best possible results for each application.
Conclusion
Damo Technology’s innovative dehydration process has proven to be a game-changer for the Hunan-based company’s isopropanol production. The technology offers a host of benefits, including energy efficiency, safety, high product recovery rates, and stable operations. Embracing Damo Technology’s advanced dehydration solution can help chemical companies optimize their processes, increase profitability, and minimize their environmental footprint.